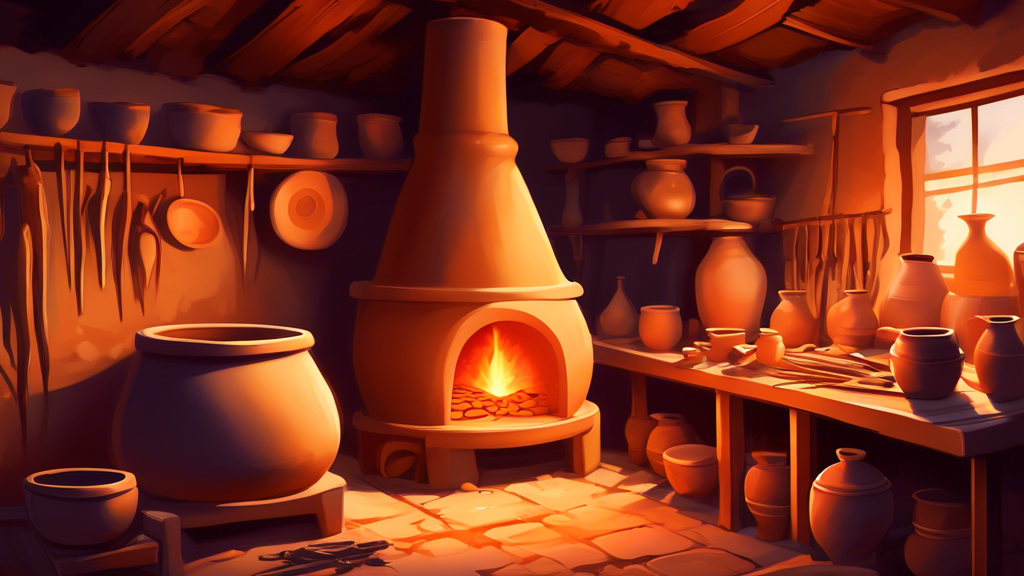
Understanding the Basics of Ceramic Firing
Understanding the Basics of Ceramic Firing
Ceramic firing is an essential process in the creation of ceramic art and functional items. It involves heating a piece of clay pottery or sculpture in a kiln at a high temperature until it transforms into a hard, durable object. This process not only hardens the clay but also vitrifies it, making it impervious to water and other fluids. Understanding the basics of ceramic firing is crucial for anyone interested in pottery or ceramic art, as it affects the final quality and appearance of the piece.
The Stages of Ceramic Firing
Ceramic firing can be divided into several stages, each critical for ensuring the structural integrity and surface quality of the piece. These stages are often referred to as bisque firing and glaze firing.
Bisque Firing
Bisque firing is the first firing process and is done at a lower temperature, typically between 1700°F and 1940°F (927°C and 1060°C). The purpose of bisque firing is to turn the clay object into a porous, yet solid, state known as 'bisque' or 'biscuit.' This stage drives off any remaining water content and organic materials in the clay, making it ready for glazing. The porous nature of bisqued ceramics allows them to absorb glazes more effectively, which is crucial for the glaze application process.
Glaze Firing
After the bisque firing and subsequent glazing, the ceramic piece undergoes glaze firing. This stage involves heating the glazed piece to a temperature high enough to melt the glaze and bond it to the bisque surface, typically between 1828°F and 2345°F (998°C and 1285°C). The exact temperature and firing duration depend on the type of clay and glaze used. Glaze firing not only strengthens the final piece but also endows it with its final colors and finish, ranging from glossy to matte, smooth to textured.
Types of Kilns
The choice of kiln can significantly influence the outcome of the firing process. There are several types of kilns available for ceramic firing, including electric, gas, and wood-fired kilns, each offering different atmospheric conditions that can affect the final appearance of the ceramic piece.
- Electric Kilns: Known for their ease of use and consistency, electric kilns are popular in schools and home studios. They provide a clean, oxidation atmosphere that is great for achieving bright glaze colors.
- Gas Kilns: Gas firing allows for both oxidation and reduction atmospheres, the latter of which can result in rich, varied surface textures and colors unattainable in an electric kiln.
- Wood-Fired Kilns: Firing with wood not only requires more skill and attention but also offers unique, unpredictable effects due to the natural ash and variable atmosphere inside the kiln.
Conclusion
Understanding the basics of ceramic firing is instrumental in mastering the art of ceramics. By carefully managing the bisque and glaze firing stages, and selecting the appropriate kiln type, artists can achieve a wide range of finishes and aesthetics in their ceramic pieces. With knowledge and experience, firing ceramics can become not just a process, but a craft in itself, opening up endless possibilities for creativity and expression.
Click this link to check out our ceramic artwork!