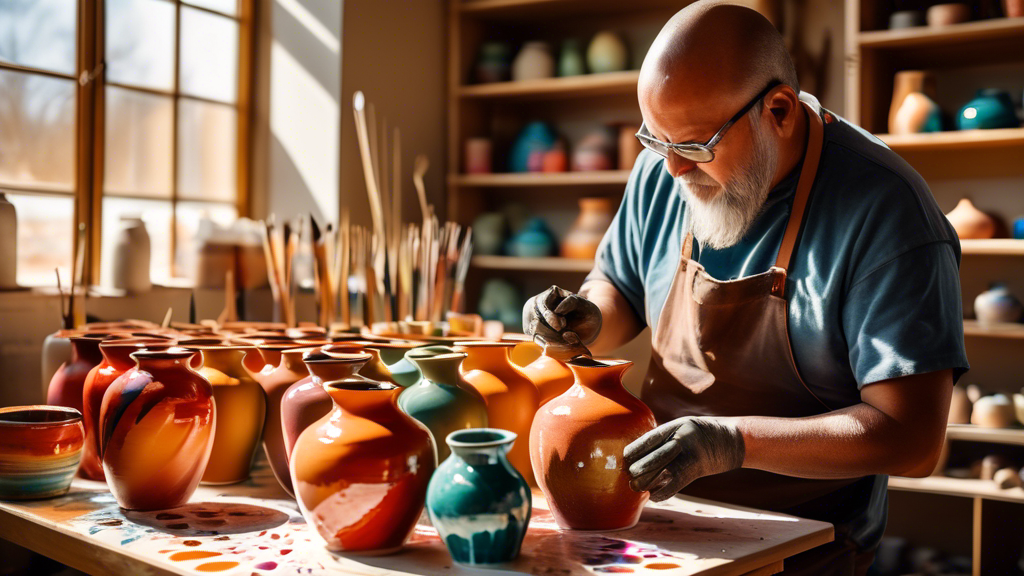
Understanding the Ceramic Glazing Process
The ceramic glazing process is a pivotal stage in the creation of ceramic art and pottery. It not only plays a crucial role in the aesthetic appeal of the final product but also serves functional purposes by making the item waterproof and increasing its durability. This intricate process involves applying a glassy layer on the surface of bisque-fired ceramic ware, which, upon firing at high temperatures, melts to form a smooth and often colorful coating. Let's delve deeper into the nuances of this fascinating process.
Ceramic glaze is essentially a glass-like substance composed of silica, alumina, and flux, along with various colorants and opacifiers to achieve different effects and finishes. Silica is responsible for the glassy nature of the glaze, alumina adds stiffness to prevent it from running off the ceramic piece during firing, and fluxes are used to lower the melting point of the silica. The choice of ingredients and their proportions can vastly affect the appearance and texture of the final glaze, offering endless possibilities for creativity.
The diversity of glazes available to ceramists is vast, with each type offering unique characteristics and visual effects. Some of the most common types include:
Glazing involves several steps, starting with the preparation of the bisque ware (unfired ceramic body) and the glaze mixture. The process can broadly be summarized as follows:
The ceramic glazing process is a testament to the blend of art and science that characterizes the field of ceramics. With a rich array of materials and methods at their disposal, ceramists have the ability to create an extensive variety of finishes on their pieces, each with its unique charm and functionality. As one delves deeper into this craft, the complexity and beauty of glazing continue to inspire both creators and admirers alike.
Understanding the Ceramic Glazing Process
The Basics of Glaze
Types of Glazes
The Glazing Process
Conclusion