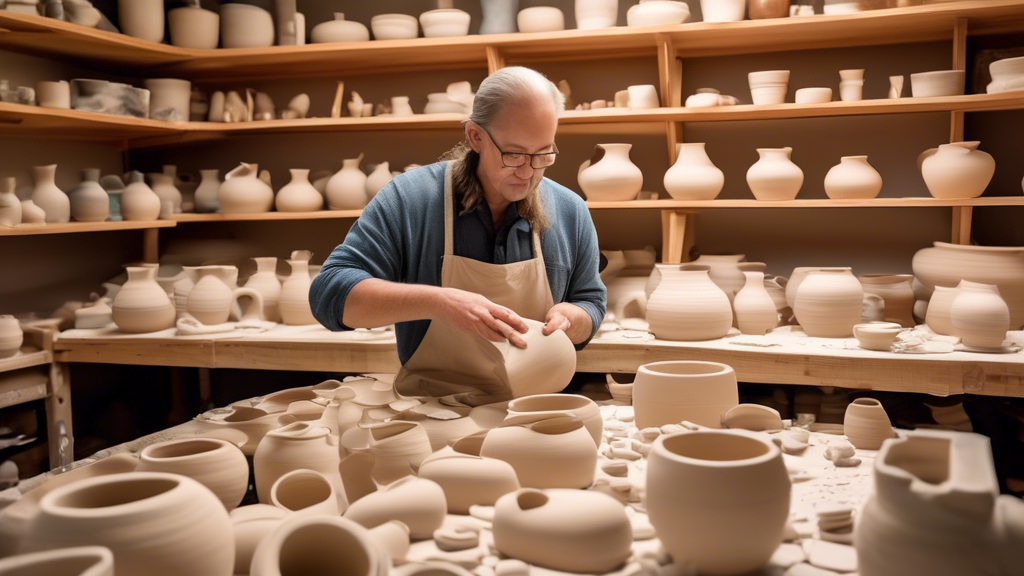
Understanding Pottery Bisque Firing: A Beginner's Guide
Understanding Pottery Bisque Firing: A Beginner's Guide
Pottery is an ancient craft that combines the elements of earth and fire to create enduring and beautiful works of art. A critical step in the pottery making process is bisque firing, a procedure that might seem daunting to beginners but is integral to the craft. This guide aims to demystify the bisque firing process, making it accessible to aspiring potters and enthusiasts alike.
What is Bisque Firing?
Bisque firing refers to the first time pottery goes through the kiln. This initial firing transforms the clay into a porous, yet solid state known as 'bisque' or 'biscuit'. Unlike glaze firing, which is the subsequent firing with glazes applied, bisque firing prepares the pottery for glazing by ensuring it is porous enough to absorb glazes. It's a crucial step in pottery that affects the final appearance and durability of the piece.
The Bisque Firing Process
The process of bisque firing begins with thoroughly dried, greenware pottery. Greenware is the term used for unfired pottery. Ensuring the pottery is completely dry is paramount; moisture in the clay can cause the pottery to explode in the kiln due to rapid steam expansion.
The kiln is then slowly heated to the bisque temperature, typically between 1730°F (945°C) and 1940°F (1060°C) for earthenware and mid-range stoneware. The slow rise in temperature is vital to prevent the pottery from cracking. Once the target temperature is reached, the kiln is allowed to cool down naturally, a process that can take a day or more, depending on the kiln size and the pottery's thickness.
Why is Bisque Firing Important?
Bisque firing serves several functions beyond transforming clay into a solid state. First, it makes the pottery more durable, allowing it to be handled more easily during the glazing process. Second, the porosity resulting from bisque firing helps the pottery absorb glazes better. Lastly, it burns away organic materials, such as paper or leaves, which potters might use in their designs, leaving behind the intricate impressions without the material itself.
Tips for Successful Bisque Firing
Ensure the Pottery is Bone Dry
Before bisque firing, make sure your pottery is bone dry. Test this by touching the clay; if it feels cold, it might still contain moisture. A longer drying time, especially for thicker pieces, ensures safety and success in the bisque firing process.
Load the Kiln Properly
When loading the kiln, ensure that pieces are not touching each other. This precaution allows for even heat distribution and minimizes the risk of pottery pieces sticking together or impeding the temperature rise.
Monitor Temperature Carefully
Use a pyrometer, a tool for measuring the temperature in the kiln, to accurately monitor the rise in temperature. Following the specific temperature curve recommended for your clay body helps in avoiding mishaps like cracking.
Patience is Key
Allow the kiln to cool down completely before opening it. Rushing this process can introduce a thermal shock to your pottery, leading to potential cracking or even breaking.
Conclusion
Bisque firing is an essential step in the pottery-making process that transforms clay into a durable and porous material, ready for glazing. Understanding this process enables beginners to better appreciate the craft and avoid common pitfalls. With patience, careful monitoring, and adherence to best practices, bisque firing can become a rewarding part of the creative journey in pottery.
Click this link to check out our ceramic artwork!