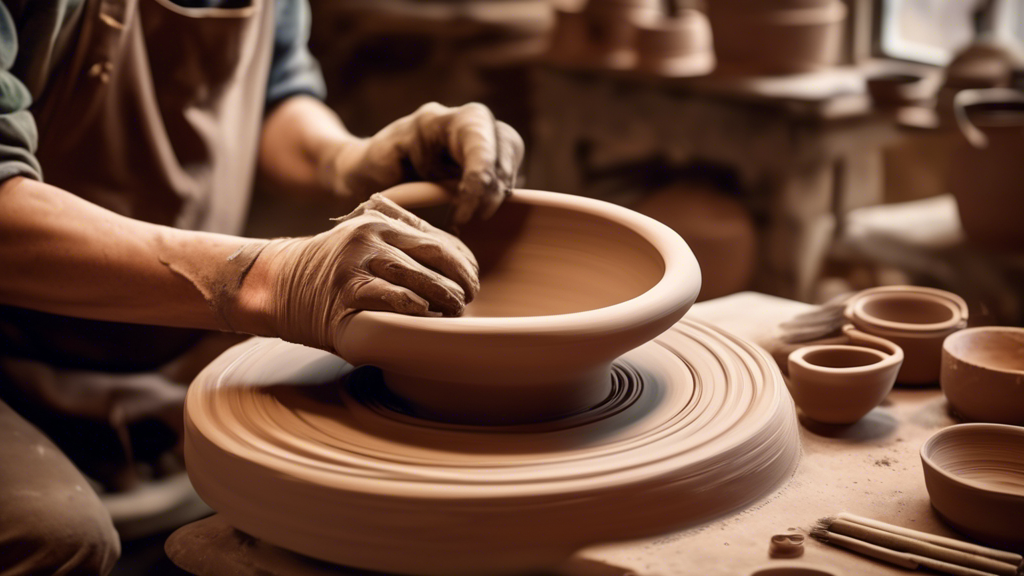
Introduction to Ceramics Making Process
Introduction to Ceramics Making Process
The art of ceramics making is one of humanity's oldest crafts, spanning thousands of years and incorporating a wide range of techniques and materials. Ceramics refer to items made from clay that permanently change when heated. The process of creating these pieces combines artistry with chemical processes, making ceramics a fascinating and complex field. This introduction aims to break down the basic steps and components involved in the ceramics making process, offering insight into how raw clay transforms into beautiful and functional items.
The Basics of Clay
At the heart of ceramics is clay, a naturally occurring material composed of fine-grained minerals. There are several types of clay, including earthenware, stoneware, and porcelain, each with its own attributes and ideal firing temperatures. The choice of clay largely depends on the desired characteristics of the finished piece, such as durability, color, and texture.
Preparation of Clay
Before shaping, the clay must be prepared. This often involves wedging, a process similar to kneading dough, which removes air bubbles and ensures a uniform consistency. Properly prepared clay is more malleable and less likely to crack during the drying and firing stages.
Forming Techniques
There are several methods to shape clay, each lending itself to different styles and forms. Some of the most prominent techniques include:
- Hand-building: This includes methods like pinching, coiling, and slab building. Hand-building is accessible and allows for a great deal of creativity and texture.
- Wheel-throwing: Using a potter’s wheel, this technique is ideal for creating symmetrical pieces such as bowls and vases. It requires skill and practice to master.
- Slip casting: Used for making complex shapes or multiple copies of a design, this process involves pouring liquid clay, or slip, into a plaster mold.
Drying
After forming, the clay object must be left to dry. This stage is critical as uneven drying can lead to cracks. The piece should be dried slowly, often taking several days, to ensure that moisture evaporates evenly.
Bisque Firing
The next step is the bisque firing, during which the dried clay pieces are fired in a kiln for the first time. This firing transforms the clay into a hard, but still porous, state known as 'bisque.' This process, typically carried out at temperatures between 900 to 1000°C, makes the pieces more durable and prepares them for glazing.
Glazing
Glazing involves applying a coating of liquid glaze to the bisque-fired piece. Glazes can vary in color, texture, and composition, offering a range of finishes from matte to glossy, transparent to opaque. After glazing, the pieces are ready for their final firing.
Glaze Firing
The glaze firing is the final stage in the ceramics making process. This firing is usually at a higher temperature than the bisque firing, causing the glaze to melt and form a glassy surface on the piece. This not only beautifies the item but also makes it waterproof and food-safe, depending on the glaze used.
Conclusion
The ceramics making process is a rewarding blend of art and science. From the initial stages of wedging and shaping the clay to the final glaze firing, each step requires patience, skill, and creativity. Whether you are a beginner interested in trying your hand at pottery or simply seeking to appreciate the complexity behind ceramic pieces, understanding the process enriches the experience. With each piece, ceramists not only continue the ancient tradition of transforming earth into art but also bring their unique vision to life.
Click this link to check out our ceramic artwork!